Electronics manufacturing is a constantly evolving field and staying ahead of the game is more important than ever. It stands to reason that choosing the right assembly technique, the starting point of any production process, is crucial to the success of your projects. Surface Mount Technology (SMT) and Through-Hole Assembly are two prominent methods, each with its own set of advantages and disadvantages. In this article, we will delve into the differences between these techniques, explore their respective pros and cons, and identify the appropriate use cases for each, ensuring that you make an informed decision for your PCB manufacturing needs.
SMT: Streamlining Efficiency
Surface Mount Technology (SMT) is a contemporary assembly technique that has gained widespread popularity due to its efficiency and versatility. In SMT, components are mounted directly onto the surface of the PCB, as opposed to being inserted through holes. This method offers several distinct advantages:
Advantages of SMT:
- Space Efficiency: SMT components are significantly smaller than their through-hole counterparts. This allows for a higher component density on the PCB, resulting in more compact and lightweight devices.
- Enhanced Performance: The shorter connection paths between components in SMT lead to reduced signal interference and improved electrical performance of the final product.
- Cost-Effectiveness: SMT assembly involves automated processes, which reduces labour costs and increases production speed. Additionally, the smaller components are often more affordable than their through-hole equivalents.
- Faster Production: SMT assembly lines can handle multiple components simultaneously using pick-and-place machines, drastically reducing manufacturing time.
- Design Flexibility: With the ability to place components on both sides of the PCB, SMT offers greater design flexibility and allows for more compact and innovative product designs.
Disadvantages of SMT:
- Complexity: SMT components are smaller and can be more challenging to handle and solder, requiring specialised equipment and skilled technicians.
- Repair Difficulty: In the event of a faulty component, removing and replacing SMT parts can be intricate and might require advanced soldering skills or even the replacement of the entire PCB.
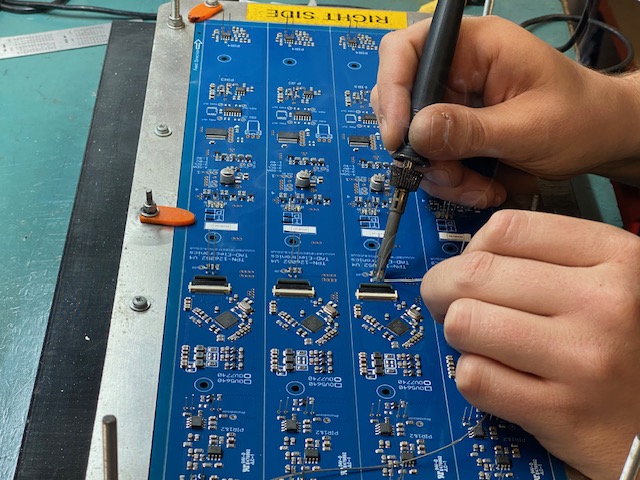
When to Choose SMT:
SMT is an ideal choice for high-volume production where efficiency, cost-effectiveness, and compact design are paramount. It suits applications like consumer electronics, smartphones, wearables, and automotive electronics.
Through-Hole Assembly: Time-Tested Reliability
Through-Hole Assembly, the traditional method of PCB manufacturing, involves inserting component leads through holes in the PCB and soldering them on the opposite side. While it has become less prevalent due to SMT’s rise, through-hole assembly still holds value in certain scenarios.
Advantages of Through-Hole Assembly:
- Mechanical Stability: Components soldered using through-hole technology are mechanically more robust and less prone to detachment due to physical stress or vibrations.
- Reliability: Through-hole solder joints tend to have higher durability, making them suitable for applications subject to extreme conditions, such as aerospace or industrial equipment.
- Ease of Repair: Faulty components can be easily replaced since desoldering through-hole parts is generally simpler and requires less specialised equipment.
- Prototyping: Through-hole assembly is preferred for prototyping and testing phases, as it allows for easier modifications and replacements during development.
Disadvantages of Through-Hole Assembly:
- Size and Space: The required holes and larger component sizes limit the PCBs density and overall design flexibility.
- Increased Costs: Manual labour, longer production times, and larger component costs can make through-hole assembly more expensive, especially for high-volume production.
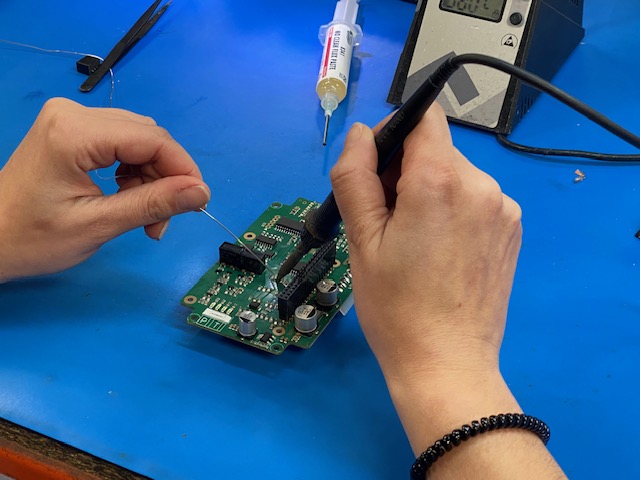
When to Choose Through-Hole Assembly:
Through-hole assembly remains a solid choice for low-volume production, prototyping, and projects demanding high mechanical reliability and robustness. Industries like aerospace, medical devices, and certain industrial applications can benefit from this technique.
Conclusion
In the dynamic landscape of electronics manufacturing, selecting the right assembly technique is pivotal to achieving your project goals. Surface Mount Technology (SMT) and Through-Hole Assembly both offer distinct advantages and disadvantages. SMT excels in efficiency, cost-effectiveness, and design flexibility, making it ideal for high-volume production of compact consumer electronics. On the other hand, Through-Hole Assembly boasts reliability and mechanical stability, making it suitable for applications subjected to harsh conditions and low-volume production needs.
Ultimately, the choice between SMT and Through-Hole Assembly depends on factors such as production volume, project requirements, budget constraints, and the specific industry. By understanding the strengths and weaknesses of each technique, you can make an informed decision that aligns with your objectives, ensuring the successful realisation of your electronic devices.
What does TAD use and why?
TAD makes use of both SMT and Through-Hole Assembly in our prototyping and manufacturing processes. It really depends on the product requirements. We will always lean to the more compact, more efficient SMT but Through-Hole will always have its place for certain components and applications.
We have two pick and place machines and Fully Automatic Stencil Printer for SMT manufacture and a dedicated through-hole area. We have undertaken staff IPC training and have years of experience with PCB manufacture. We are constantly looking for ways to improve our capabilities and experience by using Lean Six Sigma practices.
At TAD, PCBs are designed, manufactured and tested in-house all under one roof, from small prototype runs to large production batches. We have a dedicated, flexible team who have experience fabricating a large range of PCBs.
Very early on, we realised that bringing the full manufacturing process in house would lead to a much faster turnaround on prototype designs and the ability to react much faster to any production run issues.
We have had many successful projects where we have quickly taken an existing Through-Hole design, and rapidly redesigned it for SMT manufacture. In doing this we have slashed cost and manufacturing time while improving functionality.